In The Continuously Evolving Pharmaceutical Industry, Change Is The Only Constant!
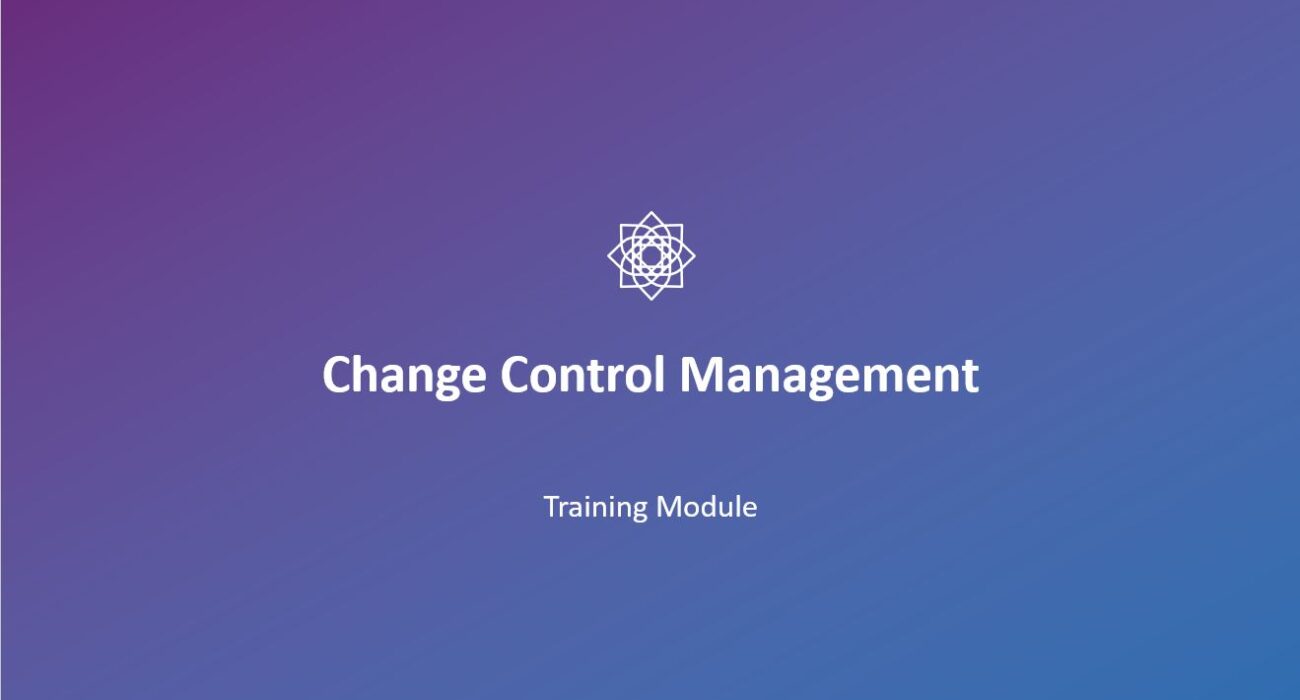
Everyone working within the industry must accept the need for a structured and documented change management process. They must first realise the benefits of having a defined change control process, to be able to effectively manage changes that impact on the medicinal products. This is a mindset shift and this free training video, with real working examples, we hope will provide you with some valuable tools in ensuring an effective implementation of a change control process and the ongoing management of change.
Video script below.
Slide 1:
Hello everyone, thank you for joining today’s session about change control and management in the pharmaceutical industry. My name is Ghada Amami, I am a Quality Assurance Associate at Inglasia Pharma Solutions.
My mission today is to refresh your knowledge about change control, hopefully give you some helpful insights about the subject. Quality and improving and implementing critical thinking is also a gap that I’m hooking to bridge.
Today, we will dive into the controls and management technicalities, but it is also important to understand that in our continuously evolving industry, change is the only constant and CCM goes beyond ticking boxes. Managing the transformation of the organization as a whole is just as important.
Slide 2:
Changes can actually arise in different ways and can carry varying levels of risk. And to navigate them, we need to ask questions. Each scenario that arises must pass through an assessment to determine its rise (which means ‘how did the change happen?’), Its cause, (why did it happen?) , and the third question is ‘what are the implications of this event’, referring to the potential impact on quality or safety or compliance.
The objective here is to be able to review, document, and migrate each situation on its own later, because a certain change can be planned, unplanned, or emergent. But what is the difference between these changes? I will guide you today through three different scenarios where change is related to one concept, the coating process in production, but had different natures.
Slide 3:
Let’s say a pharmaceutical company is deciding to upgrade one of its existing tablet coating machines .The goal here is to replace the older model with a more precise and efficient one. This upgrade has already been approved by the company’s leadership and is carefully planned in advance, so this type of change is referred to as a ‘planned’ one.This process is one where the change is thoughtfully designed ahead of time, with each step carefully outlined, and the implementation and processes are being well understood and controlled before it happens. So essentially, the company is proactively planning to minimize surprises and to ensure that the process runs smoothly. In this case, the change is considered low risk, meaning that the company has already conducted a thorough risk assessment, establishing measures to handle any potential challenge before the change actually takes place. This process requires a particular roadmap to implement the change successfully.
Slide 4:
It begins with a formal change request submitted by the person or the department suggesting the change.It can be engineering or the production team for example , detailing why this upgrade is necessary at the moment.For example, we need to improve precision in the coating process or the efficiency of the coating process. Once the request is in, the quality team conducts an impact assessment to determine how this upgrade could affect the organization, product quality, regulatory compliance, the production timelines, and this evaluation is crucial to ensure that all the necessary requirements are being met before moving forward in the process. Next comes the validation phase, where the machine undergoes a series of qualification steps to confirm its proper setup, reliable operation, and consistent performance. Basically, it’s about verifying that the machine is correctly being installed according to all the specifications, testing it under real operating conditions, and confirming that the machine is constantly producing tablets meeting all required quality standards. Operator training follows where the staff learns to operate, to clean, and to maintain the new equipment to ensure effective use of the machine. Finally, the new machine is integrated into the production process.The last step is to document the outcome, and all of these stages, from request to documentation, help the company to achieve successful change management.
Failing to accomplish one or more of these components can actually lead to surprises in the change monitoring phase, which leads us to our second scenario.
Slide 5:
After deploying the new coating machine without a proper process, technicians, for example, discovered that the coating thickness across tablets is inconsistent. In a produced batch, the tablets are not meeting the coating requirements. This is a problem because non-uniform drug release profiles undermine the product’s performance. And this is an unexpected issue, and it represents an unplanned change, as it was not foreseen during the initial planning and deployment stages of the machine upgrade. Unlike our previous scenario, this problem demands immediate corrective actions to migrate the implications and the risks. This inconsistency in coating might have serious implications for both product quality and patient safety. So it is classified as moderate to high risk according to the multiple factors influencing the risk level. For example, if the coating in question is immediate release coating, the possible implications can be aesthetic, it can be potential variation in dissolution rate, or it can be customer rejection, for example. So this case does not implicate serious health risks. The batch might face market rejection, but it has a moderate regulatory risk, as it does not necessarily mean regulatory rejection unless the dissolution fails USP criteria. Now, if the coating in question is modified release, which means extended release or delayed release, this deviation can alter drug release profiles leading to increased toxicity rate due to dose pumping if the coating is too thin, or it can mean reduced efficacy due to delayed or inefficient drug release if the coating is too thick. The risk for the coating being too thick is high as regulatory rejections are likely and the company will face market recall if detected post-release.
Slide 6:
Recognizing the potential impact of the change on product performance and quality and taking an immediate action to address the issue are required here.The first step is documenting the problem through a deviation report.Production should be temporarily paused as well, to prevent further inconsistencies and to allow for a thorough investigation.Next, a root cause analysis needs to be conducted.For example, after examining the equipment and process parameters, it is determined that the spray nozzle alignment is malfunctioning.So, this was the cause for the uneven distribution of the coating solution.Corrective actions are then implemented to resolve this issue.In the example I gave, the spray nozzle alignment, in this case, the faulty nozzle is either replaced or repaired to ensure that it functions correctly.A test batch has to be produced to verify that the problem has been resolved and that the coating thickness is now consistent and compliant with the GMP guidelines. To prevent similar issues in the future, preventative actions are introduced as well.For example, the nozzle alignment checks should be incorporated into the schedule to reduce the likelihood of unexpected malfunctions.In addition to CAPAs, SOPs should also be updated to include more detailed inspection steps before each production running in the future.
Slide 7:
The third type of change is emergent. It is important to not mistake this type for an unplanned change. Unplanned changes are unexpected events requiring immediate corrective actions. Emergent changes, on the other hand, arise continuously due to innovation, for example, or market shifts within established frameworks, and these events require adaptation and strategic alignment. Staying on the subject of coating processes, the scenario here aligns with the scope of emergent changes. For example, during production, a regulatory authority issues an urgent update mandating the use of a different coating material to reduce a certain health risk. This represents an emergent change because it’s triggered by an unforeseen and urgent scientific discovery that requires immediate attention. Given the urgency and the potential impact on product safety in this case, this change is classified as high risk. The company must act quickly to remain compliant with the regulatory requirements, and it is equally important to ensure that the transition is managed in a controlled manner. This involves conducting risk assessments, validating the new material, updating the documentation, and training the staff to prevent any compromise in product quality or regulatory compliance or patient safety.
Slide 8:
To handle this change, the first step is an immediate assessment made by the quality team. This team quickly evaluates how switching to the new coating material will impact the current production process. They need to ensure that the product integrity is maintained throughout our protocol. At the same time, the quality team needs to verify that the new chosen material aligns with the updated standards set by the authorities to prevent any compliance risks in the future. Next, the company initiates a fast-track implementation. The coating machine settings like spring rate, temperature, and airflow are all adjusted to accommodate the new material. Trial batches should also be produced and tested for key quality attributes like coating thickness and stability to confirm that the new formulation meets the required specifications. At the same time, engagement with regulatory authorities take place. The company notifies the relevant agency of the modifications, provides them with the necessary documentation, like test results and details of process adjustments to ensure smooth regulatory approval. Operator training and documentation updates follow, where staff members included in the production process receive immediate training on handling and applying the new coating material safely and effectively. Additionally, all these changes are recorded in batch records and SOPs should be revised accordingly to reflect the process.
Slide 9:
Let’s say you are making a small adjustment to the labeling that does not involve critical information.For example, you are changing the font size on the label or you’re making some adjustments to batch sizes within validated ranges.This change, this adjustment has limited to no expected impact on the product quality, efficacy and safety so,less likely to require prior regulatory approval, so often a notification of the authority is sufficient and changes can typically be implemented without waiting.
Slide 10:
In another context, let’s say you are making changes to the manufacturing processes, like introducing a new equipment or method to the sterilization process of sterile products.This is a substantial modification that can actually significantly impact the product quality, efficacy, and safety.So this change requires a prior regulatory approval before you can implement it.The submission of detailed documentation with authorities including validationstudies, risk assessment is mandatory prior to proceeding.
Slide 11:
Another category is critical changes.These are emergencies or highly significant changes that are often driven by an urgent need to address a compliance or a safety issue.For example, if you are facing an immediate recall due to contamination or adverse events,This is a safety issue.If you are making a rapid change to a label or to a package to include a safety warning mandated by a regulatory authority, this is a compliance issue.These changes are high risk to patient safety or product compliance and require immediate actions like issuing a Dear Health Professional letter that should be followed by a submission of a comprehensive post-change report and should be addressed rapidly to prevent reoccurrence.
Slide 12:
The process begins with identifying the need for a change and recognizing whether it’s planned, unplanned, or emergent, while also categorizing the impact as minor, high, or urgent. To avoid wasted efforts, the initial step of identification should be conducted by a subject matter expert, acting as the change owner , he or she raises a change control request form. Accurate early identification allows the company to assess the potential impact and prioritize the change accordingly. And the subject matter expert documents this need in the change control request form by outlining the reasons for the change, its scope, and the potential reasons and benefits of this event. Once this form is completed, it is submitted to the line manager for review. He or she, often a department expert in change control, examines the request to ensure that it aligns with the organization’s goals and determines whether the change is technically feasible and necessary at the moment. The rationale must be clearly articulated and justified. For example, if a manufacturing process is being modified to improve yield, the justification must demonstrate how the change aligns with the business objectives, whether compromising quality or regulatory compliance,or not. The next phase involves a primarily assessment conducted by the quality assurance team. They perform a high-level screening to evaluate feasibility, identify potential risks, and to ensure that the change complies with all of the regulatory standards. If it impacts how raw materials are stored, for example, QA will verify that the new method adheres to good manufacturing practices and minimizes the contamination risks. After this review, Quality Assurance logs the request into the change control database and assigns a unique change control reference number for tracking purposes. At the same time, the Quality Assurance issues a change control impact assessment form to capture detailed information about the change effects on the operations, on the safety, and on compliance. The subject matter expert then completes the change control impact assessment form by outlining the specific impacts of the change. For example, if it involves introducing a new cleaning protocol for equipment, the subject matter expert might detail how it will affect production, how it will affect staff, training requirements, and potential risks like cross-contaminations. Once both the Change Control Impact Assessment Form and the Change Control Request Form are complete, they are presented to the change review board, which typically comprises cross-functional stakeholders like quality assurance, regulatory affairs, operations, and senior management. This board evaluates the change in detail, performing a comprehensive risk assessment to identify potential hazards and to ensure that adequate migration plans are in place. This in-depth evaluation examines the technical, the operational, and the regulatory impacts of the change. If the change increases the risk of product contamination, for instance, this board might require additional safeguards like enhanced monitoring or more frequent equipment validations. And based on this evaluation, the board decides whether to approve, reject, or request modifications to the change request. Throughout this process, effective communication is crucial to ensure that all stakeholders from quality control to manufacturing to regulatory teams are all informed of the change and its implications. If the change is approved, the board will outline the required actions and timelines, the responsible personnel, documenting all of these details in the change control action execution form. Quality assurance logs these actions, deadlines, and assigned owners into the change control database to ensure full traceability. The subject matter expert acting as the overall change owner then oversees the implementation process, ensures that timelines are being met, and that resource allocation and introduced protocols are planned. Once all of these actions have been completed, the subject matter expert gathers the evidence to confirm that the change have been fully executed. This evidence is reviewed by the line manager as well to ensure that all requirements have been met. Following this, Quality Assurance conducts a final review, also known as a change verification of the updated change control database, schedules an effectiveness check to ensure that the change has achieved the intended purpose without introducing risks. So the subject matter expert then performs the effectiveness check. And if this change meets the objectives, it’s officially chosen for final approval from both the line manager and quality assurance. However, if any issues are identified during the effectiveness check, corrective actions are taken, and the process might loop back to address these issues before final closure. This ensures that the problem, like the one I mentioned in the second scenario, where the coating of tablets was uneven, won’t happen after implementing a new machine. This slide is a detailed strategy for change management, but we should not navigate it solely by ticking boxes. But also by applying critical thinking, it is not wise to allocate as much resources and time and teams just because we are changing a cleaning solvent for non-product contact surfaces, for example. Each change is different and should be evaluated and dealt with in a strategic manner.
Slide 14:
So the question we should ask here is, what makes or breaks a change management? Beyond the technicalities of documentation, assessments, and monitoring. Change management is actually a mindset. It’s a mindset of clear communication and positive change culture. This is an important point that leads us to a global problem that companies need to focus on, which is the concept of resistance to change.
Slide 15:
First, we need to talk about why people resist change in the first place. It’s rarely just about disliking new processes or technology and often about not feeling heard, valued, or prepared for what’s coming. When we notice a pushback, it’s usually a sign that we need to take a deeper look and understand the underlying fears or frustrations that our teams may be experiencing. I recognize that many of you must have been through multiple changes in short periods, whether it’s a new system, a new goal, or new procedures. This can lead to what we call change fatigue, this sense of weariness and stress from constantly adapting in the company. So when employees are tired of change, it becomes harder to them to embrace yet another new direction. This is why leadership needs to be mindful of this fatigue and ensure that the pace is sustainable and communicate clearly why each shift it’s making is necessary and how it will ultimately benefit the organization and its people. A big factor in any change effort is trust. If there is a lack of trust in leadership, it can undermine even the best plans. Some employees may feel that decisions are made at the top without understanding the challenges they are facing every day, and others might feel left out of the conversation or uncertain about where the organization is headed. Part of that trust issue can come from an overly authoritative leadership style, where instructions feel more like commands and collaborations,So if the vision is seems unclear or if the decisions appear arbitrary, people naturally hesitate. Also, sometimes companies become so focused on internal metrics and processes that they forget to highlight how these changes can benefit customers Employees can’t see the bigger purpose of the change, so it can feel like busy work for them rather than progress and they may not see a clear rationale for the change, making them even more resistant. Another striking point is the excessive paperwork, approvals and administrative tasks that slow employees down when they were not really necessary. So it’s frustrating and can make any change feel cumbersome and if companies don’t provide the adequate resources, whether it’s training, budget, or dedicated time, people will feel unprepared and overwhelmed. Employees will feel like they don’t have the necessary skills or training to adapt to the new procedures or systems, and they may lack confidence to step into the process. So companies need to also invest in a successful change management strategy. As we can see here, in all of these cases, the human factor that is usually underestimated in CCM context plays a primary role to overcome the resistance and should never be ignored.
Slide 15:
The reluctance to adapt may stem from different reasons, but it ultimately leads to the same severe outcomes on the long run. Change resistance can lead to serious quality lapses like contamination, misformulation, and packaging errors, affecting both the product safety and the public trust, and can also lead to operational failures. This poor mindset can result in hefty regulatory fines, product recalls, and even plus action lawsuits causing lasting damage to the organization’s finances and reputation.
Slide 16:
As we saw, overcoming change resistance is a long journey that won’t necessarily be successful if enough damage has been already done. Organizations need to operate with transparent communication, inclusive decision-making, process simplification where possible, and skill and training support. This is just as important as forms and approval in a successful change management.
Slide 17:
This was all.Thank you for watching.The insights and strategies we share today are integral to navigate our evolving work environment. Let’s use them to navigate change and to ensure that we are not only adapting, but also thriving.This was Ghada Amami speaking today.Thank you for joining , and see you next time.