Integrated Launch Excellence: A Checklist for Biopharma Teams
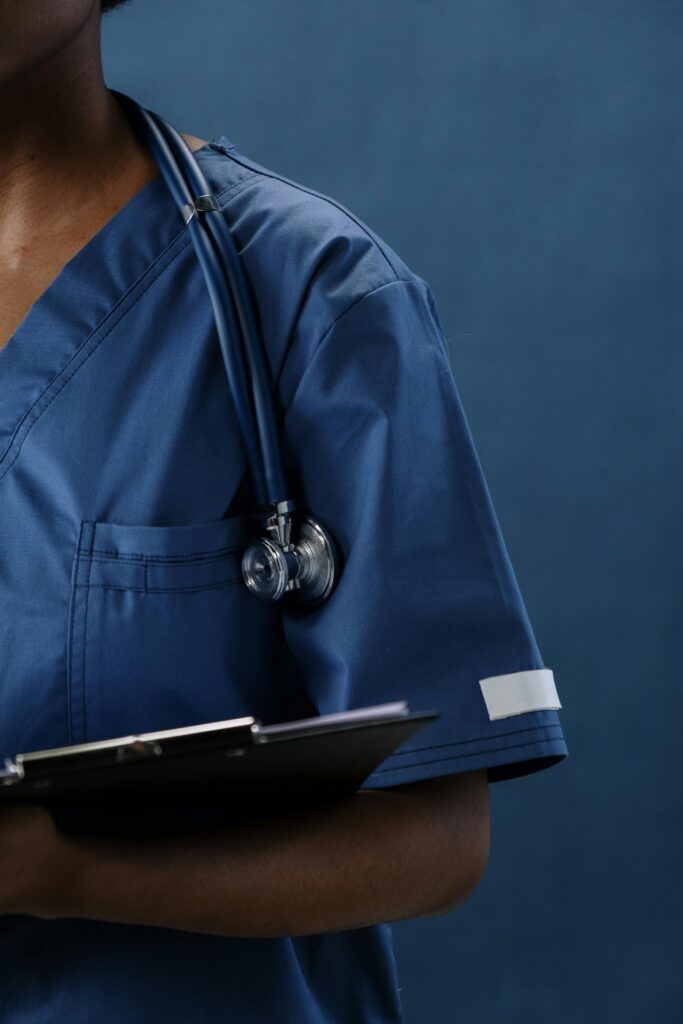
Biopharmaceutical launches are high-stakes ventures. A single misstep in regulatory filings, QA oversight or GDP compliance can delay market entry or erode trust with regulators and payers. That’s where integrated launch excellence becomes indispensable. It enables pharmaceutical and biotech companies to align cross-functional teams around shared objectives, avoid operational gaps and maintain compliance across the product lifecycle.
Here we present a structured and actionable checklist designed to support QA managers, RA specialists, supply chain leads and leadership teams in delivering consistent and compliant launches.
What Does Integrated Launch Excellence Mean for Biopharma?
Effective product launches in biopharma aren’t just about commercial success. They hinge on operational coordination, regulatory compliance and quality performance. Launch excellence in this context involves integrating manufacturing, medical affairs, regulatory, quality assurance and logistics to ensure readiness and sustainability.
A strong launch framework ensures that every function knows its responsibilities, that compliance is met before regulators raise red flags and that quality standards are reflected from supply chain readiness to product labelling.
Key elements include:
- Regulatory and quality alignment
- GMP and GDP readiness across all partners
- Scalable and structured team communication
- Clear KPIs linked to milestone tracking
Early Phase Launch Planning (24–36 Months Out)
Starting too late is the first avoidable mistake in launch planning. Early-phase planning should focus on cross-functional alignment, document readiness and understanding regional regulatory expectations.
1. Team and Governance Structure
Create a structured governance model that includes QA, regulatory, logistics and commercial leads. Launch leadership should meet biweekly by default, increasing frequency as the launch approaches.
Your team should define:
- Primary roles and delegated authorities
- Decision-making pathways
- Approval timelines for all departments
2. Regulatory Landscape Analysis
A deep dive into target markets helps prevent delays at the submission or market access stage. Early identification of requirements allows teams to build regulatory activities into launch timelines.
3. Quality System Preparation
Ensure existing systems can support the product type and intended scale. That includes:
- Computer System Validation (CSV)
- Change control processes
- CAPA management systems
One often-overlooked point is that regulatory submissions frequently fail due to formatting errors or incompatible data files, not just content.
Pre-Launch Activities (12–24 Months Out)
This is where integrated launch excellence shifts from theory to practice. Documentation, validation and partner readiness become the focus. At this stage, quality systems must be stress-tested, suppliers audited and all technical protocols refined to regulatory expectations. Every decision, from raw material sourcing to packaging line readiness, has to align with both market timelines and compliance frameworks.
1. GMP/GDP Supply Chain Audits
Validate that all third-party partners meet applicable standards. This includes raw material suppliers, CMOs, logistics firms and even cold chain providers.
Assess partners based on:
- Facility audit history
- Staff qualifications
- Documentation control systems
2. Process Validation Strategy
Include Design Qualification (DQ), Installation Qualification (IQ), Operational Qualification (OQ) and Performance Qualification (PQ) phases. Align the process validation strategy with your product’s risk profile and intended regulatory market.
A solid validation package includes:
- Equipment calibration logs
- Cleaning validation SOPs
- Analytical method validation results
3. Manufacturing Transfer Readiness
Confirm that receiving sites, whether in-house or outsourced, are trained, staffed and qualified to manufacture and test the product to specification. One under-discussed risk is underestimating how changes in excipient or packaging supplier can trigger revalidation needs and new filings in certain regions.
Final Preparations (3–12 Months Out)
As the launch draws near, attention shifts to execution readiness. This is the time to test processes, train teams and tighten quality assurance practices. Any lingering gaps in documentation, system performance or personnel capability must be identified and resolved. Regulatory teams should be preparing for final authority responses while operational teams simulate full production and distribution cycles under real conditions.
1. Launch Site Readiness Checks
Perform mock inspections, internal audits and dry runs of the production and QA handoffs. Run-throughs help uncover bottlenecks or control gaps before real-world pressure sets in.
Key focus areas:
- Document review cycles
- Lot release procedures
- Product labelling and artwork control
2. Regulatory Filing and Labelling Approvals
Track submission dates, anticipated response times and possible objections. Ensure that the label content is consistent with the approved indication, especially in multi-region launches where wording requirements vary.
3. Training and Competency Validation
Cross-functional training must extend beyond SOPs. Include product-specific modules, deviation management and adverse event handling. Teams often overlook refresher courses or assume prior experience is sufficient. This can be flagged during inspection.
Post-Launch Performance (0–6 Months Post-Launch)
The first six months are a performance litmus test. Small issues quickly snowball into regulatory challenges, recalls or market access setbacks if left unchecked. This period demands close monitoring of QA metrics, rapid response protocols and consistent communication between departments. Any deviation, delay or complaint should trigger immediate root cause analysis and corrective action. It’s also the time to validate whether assumptions made during planning are holding up in real-world conditions.
1. KPI Monitoring and QA Audits
Define success metrics across QA, regulatory and manufacturing. Conduct QA audits and trending reviews monthly.
Sample metrics include:
- Batch rejection rates
- Deviation closure time
- Product complaints volume and response time
2. GDP Compliance in Distribution
Ensure all transportation partners maintain cold chain logs, have contingency protocols for delays and document each step from dispatch to delivery. An often-overlooked failure point: inconsistencies between the temperature logs and the shipping records, particularly for biologics.
3. Real-Time Feedback Loops
Set up structured check-ins with frontline teams to identify issues, propose adjustments and document corrective actions.
Continuous Launch Optimisation (6+ Months Post-Launch)
Launch doesn’t stop with the first sale. A successful strategy must adapt to real-time data, market dynamics and regulatory feedback.
1. Lifecycle Management Integration
Start planning for variations, new indications or formulation updates. Coordinate with regulatory and QA teams to prepare for new filings or post-approval commitments.
2. Manufacturing Scalability
Scale production without compromising quality. Integrate change control and deviation management systems into the expansion process.
Expansion checks should cover:
- Material qualification at new volumes
- Equipment calibration scaling
- Staffing and shift pattern adaptations
3. Lessons Learned and Documentation Audits
Run formal debriefs involving every department. Evaluate what worked, what didn’t and which processes were misaligned. Document everything. Regulatory authorities often request these summaries during pre-approval inspections for future product launches.
Final Launch Excellence Checklist
Before a biopharmaceutical product is released into the market, a precise, quality-assured and regulation-compliant checklist must be fulfilled. This is a final safeguard against launch delays, QA nonconformities and post-market failures. A missed item at this stage can result in withdrawal notices, inspection observations or distribution holds.
This checklist brings together all functional areas – quality assurance, regulatory compliance, GMP readiness and GDP logistics – into one aligned decision-making moment.
- Regulatory Filings: All submissions finalised, acknowledged by relevant authorities, with no outstanding requests for information (RFIs) or clock-stopping issues.
- GMP/GDP Audit Reports: Internal and third-party GMP audits completed; GDP compliance confirmed for logistics, with approved contingency plans documented for each distribution hub.
- Validation Packages: Full execution and documentation of DQ, IQ, OQ, PQ protocols, analytical method validations, cleaning validation and system suitability checks – cross-verified by QA leadership.
- Quality System Updates: Any new SOPs related to the product launch have been implemented, reviewed and embedded into the QMS. Electronic systems (e.g., QMS software) should reflect updated workflows.
- Risk Management Reviews: FMEA assessments conducted for manufacturing and distribution; all critical failure points addressed with CAPAs in place and tested for effectiveness.
- Staff Training Records: All teams, QA, production, packaging, logistics and customer service have completed launch-specific and role-specific training. Competency checks documented and approved.
- Product Labelling and Artwork Controls: Artwork approved by both RA and QA; mock-ups matched against batch records; serialisation and tamper-proofing validated as per regional requirements.
- QA Batch Release: Product passed all in-process controls and final QC testing. Batch release authorised and signed off by designated QA personnel. Retention samples stored and labelled properly.
- Distribution Network Readiness: Shipment routes validated. Temperature monitoring devices calibrated and loaded. Third-party logistics partners briefed on chain-of-custody documentation.
- Recall and Deviation Procedures Ready: Procedures tested in tabletop scenarios or drills. Teams trained to respond immediately to deviations, temperature excursions or out-of-spec batches.
- Launch Readiness Reviews Signed Off: All cross-functional departments have formally signed off on their readiness. Minutes and signatories are stored in audit-ready format.
- Communication Protocols Activated: Internal escalation pathways defined; external comms plans in place for HCPs, regulators and supply partners in case of post-launch issues.
- Post-Launch Surveillance Tools Deployed: Complaint logging systems configured. Signal detection protocols in place. QA and PV teams aligned on reporting timelines and thresholds.
Take the Guesswork Out of Biopharma Launches
If your team is planning a new product introduction and is unsure where the gaps may be, Inglasia brings clarity, structure and precision. From pre-approval validation to GDP logistics auditing, Inglasia is trusted by pharma and biotech leaders looking to get their launch right the first time.
Schedule a consultation today to walk through your launch framework with experts who know the risks and how to mitigate them. Let’s make your next product release your most successful yet.